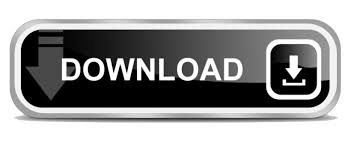
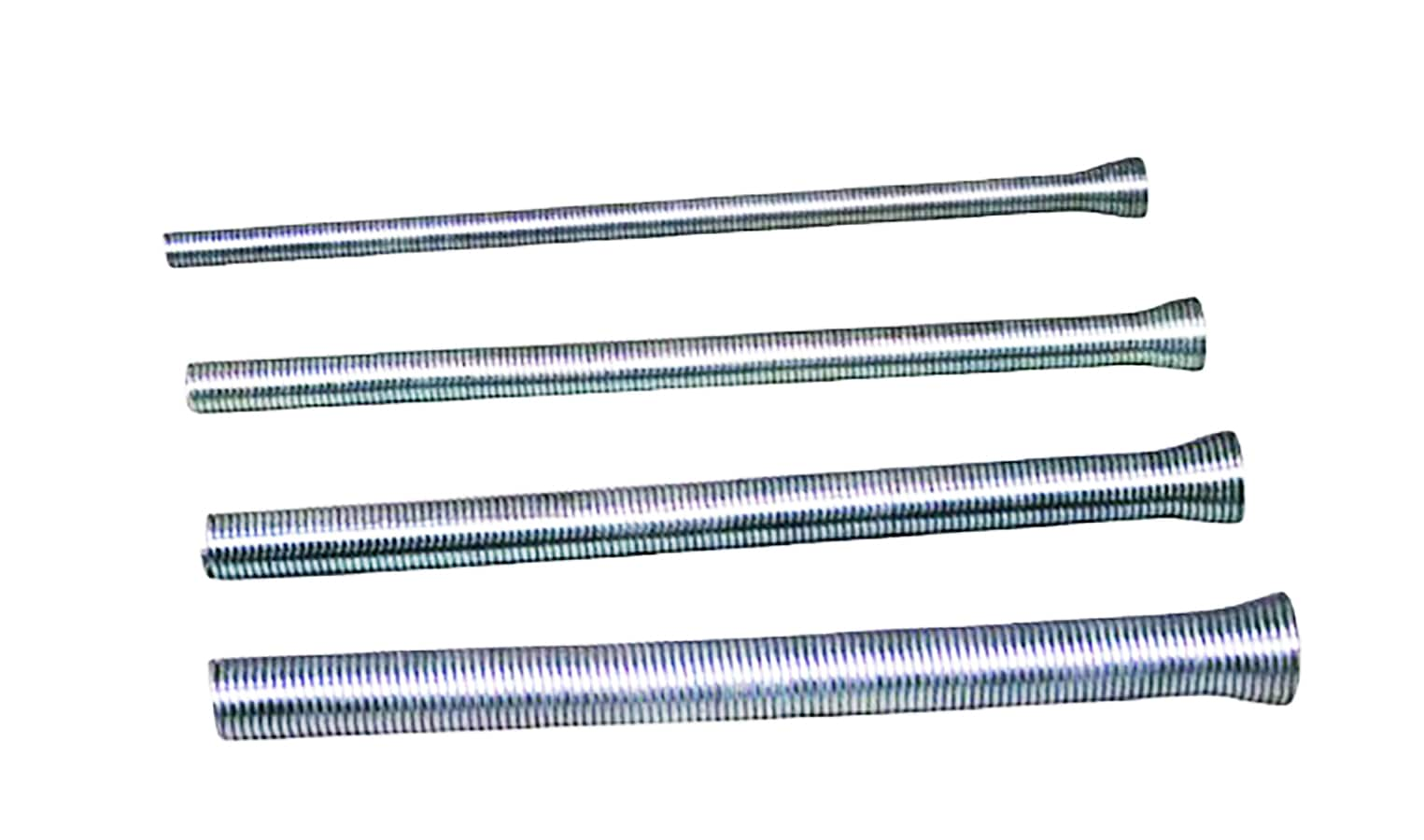
- #Copper tube bending how to#
- #Copper tube bending full size#
- #Copper tube bending full#
- #Copper tube bending plus#
Our offset is 5” (use the correct number for your machine from the table in the 101 section) for a 2015 to current machine for a 4.5” CLR die, so hang 0.5” of tube out of the end of the clamp block and bend 90 degrees. We want a 10 inch leg with a 4.5” bend, so we need 5.5” of straight tube (5.5″ tube, 4.5″ in the bend since it’s a 4.5 CLR die). We’re going to bend from one end to the other, starting with the 90 degree bend (following the same layout from the 201 section). The following paragraph is a VERY DENSE explanation of another way to bend the same shape drawn above in Bending 103. Starting From One End of the Tube, Not the Middle This may be okay if you want to keep things simple and don’t mind a little waste. Doing that would result in you having a longer cut length.
#Copper tube bending full#
If you cut your tube to the full “sharp corner” length, You will have to cut the ends after you are done. Repeat this process until you are done bending your layout. If your second clamp block location doesn’t seem to be as close to the bend as you drew it, you may draw it closer and maintain as much accuracy as possible.ġ0. Now is the time to account for any stretching that may take place. Remove the tube and lay it on top of your layout. Make your bend per machine instructions.ĩ. Load into the bender (from front) until the clamp block line is on the front face of the clamp block.Ĩ. Measure out from center and draw your clamp block lines on the tube (7.75” and 10.75” in the example above).ħ. bend length which can be easily calculated using the numbers given in the 102 section above.Ħ.
#Copper tube bending plus#
The length is simply all the straight lengths from the layout added up, plus the “take up” A.K.A. Now cut your tube to length, and put a mark in the very center of your tube. The process is good, but the numbers are not longer correct for just the bend offsets. NOTE – This layout is shown with some outdated bend offsets. What you will now have is the locations where you clamp the material in the machine to put the bends where they are in the layout.
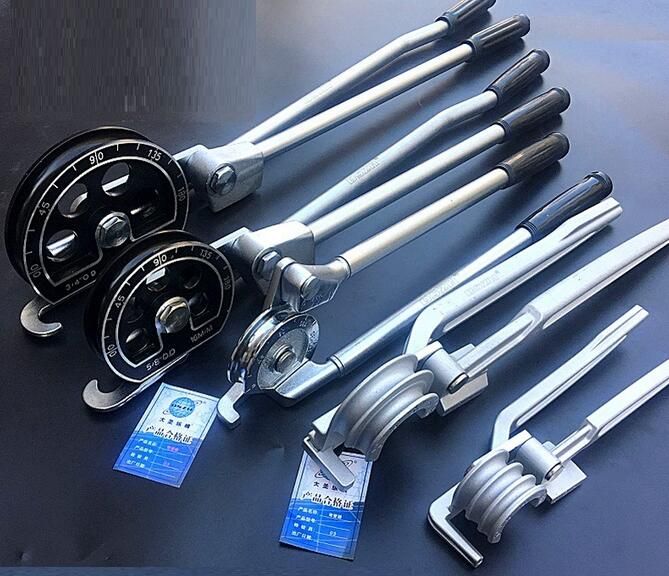
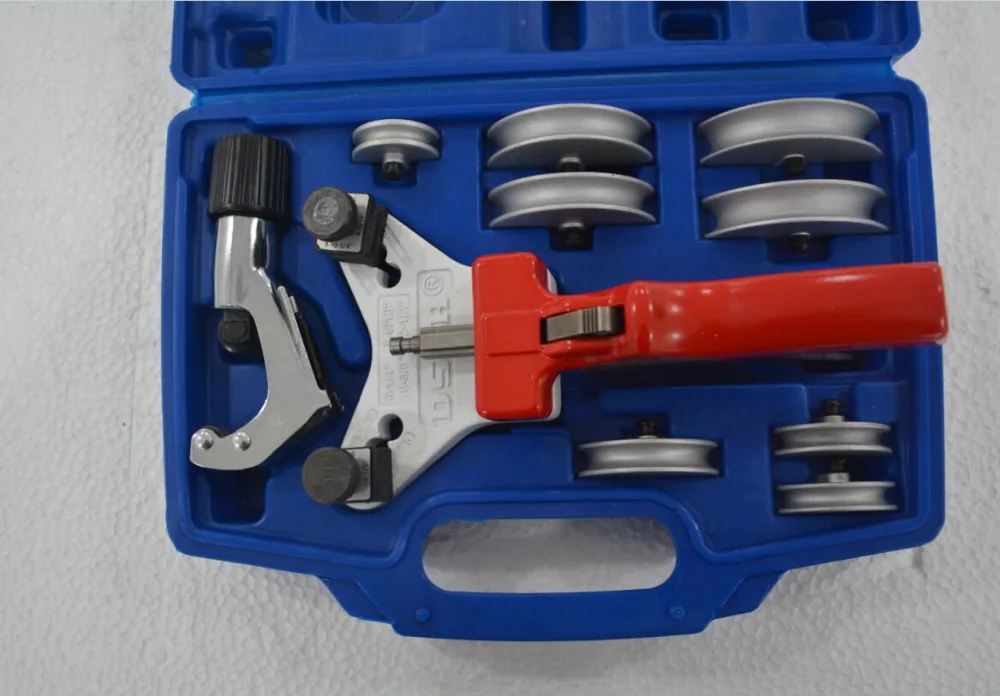
This is where we will start fabricating from.
#Copper tube bending full size#
#Copper tube bending how to#
Now that you know how to calculate the length of a bend, and where a bend will start based on where you clamp it in the machine, you can easily put a bend in the middle of a piece of tubing.
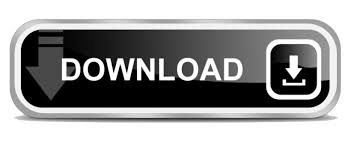